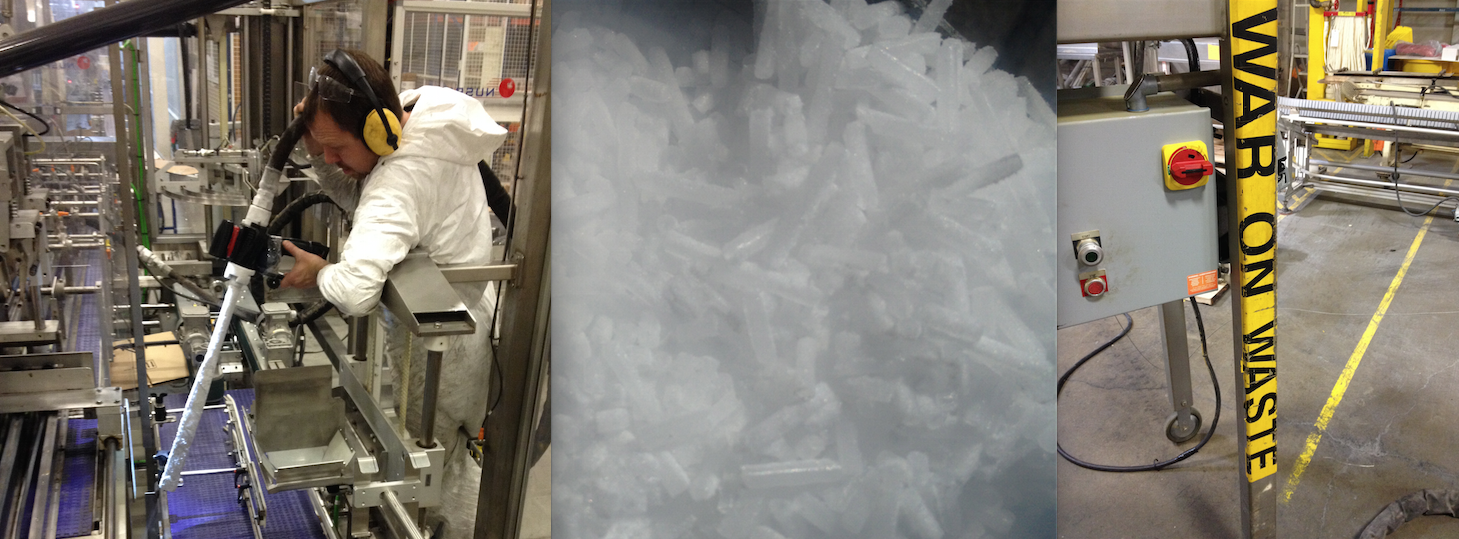
First thing that everyone should understand, is that all forms of abrasive blasting have their own individual merits. We’re not here to tell you that dry ice blasting is the ‘be-all-end-all’ of contaminate and surface prep solutions. Dry Ice Blasting is, however, in a league all it’s own and it’s the fastest most economical means of cleaning process equipment around.
60%-80% faster, actually. We can reach places your rags, picks, and brushes just can’t; and we do it a break neck speeds.
Although it’s classed as an abrasive blasting method, it’s virtually non-abrasive. It’s only abrasive to those surface softer than the dry ice pellet (or snow flake) itself, and dry ice pellets are no harder than your finger nail. Now test your contaminate with your finger nail and you’ll have a better idea of what dry ice blasting is capable of.
Dry ice blasting is “in league all it’s own” not due the hardness of the media, but due to the he simple physics of the entire process……….
About the Process
Dry Ice Blasting is a process in which hard pieces of frozen CO2 pellets are shot at a surface with air or other gases. The extreme cold (-79°C -109°F) causes the contaminant to become brittle by causing a thermal differential between the layer of debris and the substrate. The cold shrinks the debris causing it to contract, and weaken the bond with the substrate, which when combined with the micro- explosions created by the sublimation process (800x/ms), the contaminant explodes from the surface without altering or abrading the profile of the underlining substrate. CO2 pellets can strip paints and remove grease and oil. The pellets can be generated in different sizes and propelled at various speeds to increase cleaning rates or reduce surface damage.
Alternatively, soft “snow flakes” of dry ice are used to clean surfaces. CO2 snow is very effective at removing fine particles. It has been used for cleaning optical components, gyroscopes, thin film mirrors, and other delicate surfaces. This method also has the capabilities of removing thin fluid layers, flux, and fingerprints. “Snow” will not remove rust, paint, greases, or heavy oil layers. The process is best suited for pellet cleaning.
The biggest advantage of the dry ice blasting is it’s superiority when cleaning by disinfecting, and leaving no residue behind which is why the use of dry ice meets CFIA, FDA, USDA & EPA guidelines. Secondly, but not least of all, that because the blast media vaporizes upon contact, it protects any surrounding equipment from accidental contamination, and it leaves no secondary waste to dispose of afterward.
Safety considerations include:
- ventilation when working in confined spaces
- eye/skin protection
- ear protection (noise levels may reach anywhere from 20 – 120 dB
Comprehensive Descriptions of Dry Ice Blasting (PDF)
How Dry Ice Is Made…
Further Reading: EIGA – Environmental Impact of Dry Ice (PDF)
Dry Ice Blasting the most effective means of removing loose surface and tightly bonded contaminants. The process is environmentally friendly, non-conductive, non-abrasive and most importantly, non-waste generating. Dry Ice Blasting’s non-waste-generating properties mean you can clean and be back on-line 60% faster than ANY other cleaning method around, and when you choose EcoJet Dry ice Blasting you can be sure that the job gets done right, and without disrupting the regular operation of your facility…
Dry Ice Blasting vs…
Sand Blasting
Sand is the most well-known form of abrasive blasting. The highly abrasive qualities of the blast media makes it an effective candidate for stripping paint, and for preparing surfaces for paint by changing the profile of the substrate. This also means that sand is not a very good candidate for the cleaning of delicate equipment or surfaces. Like all other forms of abrasive blasting, sand blasting creates secondary waste that, in most cases, must be treated as a hazardous waste.
Other forms of abrasive blasting that can be compared, in part, to sand blasting: soda, iron, glass, bead, walnut, corn cob, etc.
Soda Blasting
Soda Blasting is generally an effective cleaning method. However, Soda Blasting, like all open blasting, creates a great deal of secondary waste. Often, the time spent blasting is matched, if not doubled by the time it takes to clean up the extra waste soda blasting creates. In fact, the residue and waste left behind by soda blasting can adhere to wood and other substrates being blasted. When Soda Blasting, all plant life must be protected from exposure when blasting. There is also some debate as to the effects soda blasting can have on the PH levels of the soil it comes into contact with after blasting.
High Pressure Water Blasting
While it’s among the fastest methods of cleaning, water blasting nevertheless has limited applications. On steel surfaces, for example, it cannot create any specific surface profile, which is a key parameter in paint performance. Also, the use of water induces flash rusting, which makes paint or coating application more difficult and risky. Furthermore the use of water blasting on production equipment including automated welding lines, presses, motors and machine tools can result in severe electrical problems. Many customers tell us that water blasting is the quickest way to burn up a motor.
Solvent Cleaning
Most solvent cleaning processes involve substances that are detrimental to the environment and worker safety. When solvents are used to dissolve unwanted surface materials, a subsequent flushing, rinsing or hand tool operation is frequently required to remove the dissolved materials. Equipment must often be disassembled or extensively prepared prior to the solvent cleaning to protect sensitive portions. Solvent management and disposal are also costly issues for businesses.
Power Tool Cleaning
Power tool cleaning can provide a quick solution for flat, simple geometries-but it can also damage or wear down surfaces.
Hand Tool Cleaning
Quick, easy tasks that would take too long to set up for more mechanized approaches are often accomplished by employees who clean only defined areas and use specified hand tools that may end up damaging your equipment.